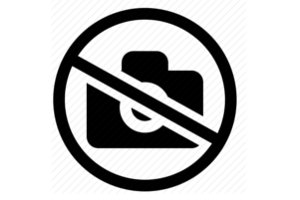
L'usine sidérurgique d'Hagondange est un ancien complexe sidérurgique dans la vallée de la Moselle, situé sur les communes d’Hagondange et de Talange. Construite par August Thyssen, l'usine démarre en 1912 avant d'être paralysée par la Première Guerre mondiale et confisquée par les Français en 1918. Elle devient alors l'usine de l'UCPMI, un groupement de consommateurs de produits sidérurgiques mené par Louis Renault.
Remarquablement cohérente et moderne grâce à la rapidité de sa construction, l'usine reste jusque dans les années 1950 une référence pour la sidérurgie française. Mais, spécialisée dans les produits longs, marginalisée par son actionnariat et figée dans sa conception initiale, elle s'avère trop obsolète et sous-dimensionnée pour survivre à la crise de la sidérurgie. Elle est ainsi sacrifiée au début des années 1970 au profit de l'usine sidérurgique de Gandrange-Rombas, et ferme en 1985.
Quelques années après, l'usine a totalement disparu ; le parc d'attractions Walygator Grand Est est construit sur le terrain occupé par l'usine. Cependant, en 2019, une activité sidérurgique subsiste à proximité, avec l'aciérie et la forge issues d'Ascometal.
Les premiers projets d'installation d'une usine sidérurgique se concrétisent en 1899 : la jeune S.A. des Minières et Usines de Pierrevillers achète 35 ha de terrain à proximité de la gare de Hagondange pour y édifier des hauts fourneaux. En 1902, la S.A. des Minieres et Usines de Pierrevillers est mise en liquidation. Le , August Thyssen en rachète les mines de Pierrevillers, Zukunft et Fèves, dont les concessions s'étalent sur 7,94 km2. Cette acquisition s'inscrit dans une stratégie d'achats de concessions minières :
Ainsi, en 1912, August Thyssen contrôle 21,55 km2 en Meurthe-et-Moselle et 31,87 km2 en Moselle annexée, ce qui en fait le plus gros propriétaire rhénan de mines dans le bassin ferrifère lorrain.
Quant à l'usine sidérurgique elle-même, sa conception mûri à partir de 1905. Les plans définitifs sont établis en .
Les travaux commencent avec la construction, en 1906, d'une cimenterie d'une capacité de 600 000 barils/jour, qui démarre en 1910,. Le chantier, dirigé par Franz Dahl, commence réellement en sur un terrain de 11,28 km2 situé à proximité de la voie ferrée de Metz-Thionville et de la Moselle : « Les travaux, qui durent 22 mois, sont gigantesques. » Les bâtiments couvrent 250 ha. Le léger dénivelé naturel du terrain de 5 × 1,2 km atteint 20 m, et permet d'optimiser les flux logistiques,.
L'usine, qui est la dernière de la vague de création d'usine sidérurgiques construites pour valoriser la minette lorraine avec le procédé Thomas, intègre tous les derniers raffinements technologiques. L'emploi de l'électricité est généralisé (la puissance des génératrices installées atteint 36,6 MW), le gaz de haut fourneau est systématiquement valorisé et les installations sont généreusement dimensionnées. La logistique est à l'échelle du complexe : en 1921, 27 locomotives roulent sur 127 km de voies ferrées privées et les accumulateurs de minerai peuvent stocker 75 000 t.
Le , la Stahlwerk Thyssen AG est fondée, avec un capital de 1 million de marks-or. Les ambitions sont prodigieuses : le projet initial de 4 hauts fourneaux est rapidement porté à 6 construits, et les réservations sont prévues pour 2, voire 3, hauts fourneaux supplémentaires. Chaque four (600 m3 chacun) peut alors produire 300 tonnes de fonte par jour, capacité qui atteindra 500 tonnes dans les années 1930, et 1 000 tonnes en 1979. Le complexe aurait pu être épaulé par 3 autres divisions identiques implantées au sud de l'usine, vers Maizières-lès-Metz…
La fondation de l'usine va métamorphoser la ville de Hagondange : en 1910, elle compte 1 727 habitants. Quatre ans après, plus de 5 000 habitants y vivent. Beaucoup sont des techniciens arrivés d'Allemagne, dont l'expertise est indispensable à la marche de l'usine.
Le , les deux premiers hauts fourneaux sont mis à feu. Ils ont été précédés par la centrale électrique et sont, logiquement, suivis par l'aciérie Thomas et le train dégrossisseur. Les 4 hauts fourneaux suivants sont démarrés dans la foulée. Pour cette première étape, l'usine se limite à la fabrication de demi-produits qui sont expédiés dans les usines allemandes.
La fonte produite par ces hauts fourneaux est envoyée dans 2 gros mélangeurs de 750 t chacun, puis affinée dans deux aciéries, l'une constituée de 5 convertisseurs Thomas de 30 t, et l'autre de 2 fours Martin. L'aciérie Martin est alors la seule de Moselle avec celle de Rombas. Elle comporte un four fixe de 60 t et n four oscillant de 80 t, les gaz de chauffage provenant d’une batterie de 11 gazogènes. Une aciérie électrique à 3 fours (deux fours Héroult de 12 t et un de 20 t) complète l'ensemble . Un atelier d'agglomération, constitué de 2 fours tournants Fellner-Ziegler, recycle les fines. Coté laminoirs, l'usine comporte un puissant train à blooms électrique (2 moteurs de 5 500 ch chacun) en amont d'un train finisseur (9 cages de laminage de divers types) et d'ateliers divers de parachèvement.
La capacité finale de l'usine, prévue à 1,2 Mt, dépasse les possibilités d'approvisionnement des mines de Thyssen. En 1913, celui-ci doit acquérir des concessions supplémentaires et se fournir en minerai sur le marché. L'usine a été pensée comme un complexe aussi énorme que moderne :
— Rasch & Feldman, August Thyssen und Hugo Stinnes: ein Briefwechsel 1898 - 1922
La guerre met un terme à ces projets d'expansion. L'usine est même complètement stoppée en . Elle redémarre mais, paralysée par la réquisition des locomotives, la mobilisation d'une partie de la main-d'œuvre et les restrictions dues à la guerre, l'usine tourne au ralenti.
En 1918, l'entreprise est mise sous séquestre. La capacité de l'usine est alors estimée à 440 000 t/an de fonte et 400 000 t/an de lingots, 10 000 ouvriers y travaillent. La taille et l'efficacité de l'usine sont paradoxalement un handicap : sa production, initialement destinée à l'Allemagne, pourrait déstabiliser le marché français. Elle pourrait même soutenir une guerre des prix dommageable aux sidérurgistes dont la modernisation a été interrompue par la guerre. Mais elle a souffert de la guerre, et la présence d'experts allemands y est aussi indispensable qu'indésirable,.
C'est dans ce contexte qu'est créée, le , l'Union des Consommateurs de Produits Métallurgiques (UCPMI), association de clients de la sidérurgie menés par Renault qui souhaitent, grâce à cette usine, peser sur les prix et la qualité du marché. L'UCPMI se voit ainsi adjuger l'actif industriel de Thyssen pour 150 millions de francs, ainsi que la fonderie Saint-Benoît. En 1919, elle achète également la mine Sainte-Barbe d'Algrange.
Mais, bien qu'opérationnelle, l'usine n'a pas encore atteint sa maturité. Elle est de plus fortement dépendante du coke de la Ruhr, comme des usines de parachèvement allemandes. En 1927, commence ainsi la construction d'une cokerie dotée de deux batteries de 33 fours à coke, avec les annexes correspondantes pour la logistique ferroviaire et fluviale du charbon et du coke. Cette cokerie est dimensionnée pour produire 1 900 t/j de coke, ce qui correspond alors à l'approvisionnement de 3 hauts fourneaux.
Cet investissement est complété en 1929, par le creusement du canal des mines de fer de la Moselle (CAMIFEMO), avec un port fluvial dédié. L'idée est de mieux connecter l'usine à ses fournisseurs en coke de la Ruhr, et d'accéder au marché sidérurgique allemand. En 1932, la section du canal entre Metz et Thionville est ouverte aux péniches de 350 t. Mais les industriels allemands s'opposent logiquement à ce projet, et la canalisation de l'aval de la Moselle reste suspendue jusqu'au début des années 1960, quand la CECA fait de la canalisation de la Moselle un projet prioritaire.
En 1930, les hauts fourneaux sont encore présentés comme étant « les plus modernes d'Europe ». Mais si l'usine s'avère efficace pour la production en masse d'aciers de commodité, la production d'aciers spéciaux la désorganise. C'est ainsi qu'est fondée cette année-là la SAFE (Société des Aciers fins de l'Est). Avec 2 convertisseurs Martin, cette dernière produit certaines spécialités que lui laisse l'UCPMI.
Les années 1930 sont marquées par les soubresauts économiques et politiques. La Grande Dépression se traduit par la fermeture en 1931 de la mine de Pierrevillers, connectée par chemin de fer à l'usine, et l'année 1932 se distingue par une production très basse. L'actionnaire s'oppose toutefois à toute participation aux cartels qui auraient pu aider l'usine.
En 1932, Louis Renault crée la SAFE (Société des Aciers Fins de l'Est) pour fournir les tôles de ses voitures. Il choisit de s'installer à Hagondange pour associer étroitement sa nouvelle usine à l'UCPMI, handicapée par sa taille dès qu'il faut produire des aciers spéciaux. En 1952 s'ajoutera à l'aciérie, la forge pour les pignons (forge à chaud) et les arbres (forge à froid) de ses boîtes de vitesses. C'est une entreprise distincte mais étroitement associée à l'usine sidérurgique.
À la veille de la Seconde Guerre mondiale, l'usine est restée un ensemble remarquablement cohérent et l'année 1939 correspond à une production exceptionnelle. L'aciérie Martin comporte 2 fours de 100 t (1 oscillant et 1 fixe) et 1 four fixe de 90 t. À cette époque, les gazogènes servent rarement : la marche normale des convertisseurs est assurée avec du gaz mixte (mélange régulé de gaz de haut fourneau et de gaz de cokerie).
Après la Seconde Guerre mondiale, l'usine est encore un des fleurons de la sidérurgie française. Mais cette position vient plus de l'obsolescence de ses concurrents que des qualités intrinsèques à l'usine. Georgette Elgey résume l'évaluation de Pierre Mendès France : « Dans ce secteur, le retard était effarant. En 1947, l’aciérie la plus moderne de France était Hagondange construite en 1910 par les Allemands en Lorraine. »
Bien que l'usine reste à l'écart des grands investissements et des regroupements qui concernent alors essentiellement la sidérurgie des aciers plats, quelques investissements viennent compléter le site dans les années 1950 :
En 1955, l'UCPMI emploie plus de 5 000 personnes,. Jusque dans les années 1960, l'outil est maintenu à niveau. L'agrandissement des hauts fourneaux permet d'en éteindre quelques-uns sans diminuer la capacité globale du site qui peut atteindre 100 000 t/mois de fonte (la production annuelle restant de l'ordre de 600 000 à 800 000 t/an). Ainsi HF6 est-il arrêté vers 1960/61, alors que le HF2, maintenu en réserve, cesse de produire en 1973 et n'est alors plus réparé. Dans les années 1970, la marche à 4 hauts fourneaux permet l'autarcie de l'usine, mais leur capacité augmentant encore, la fonte excédentaire est envoyée aux usines de Gandrange et de Florange, le flux s'inversant pendant les marches à 3 hauts fourneaux.
En 1963, l'UCPMI qui produit 700 000 t/an est considérée comme une « petite société lorraine ». À l'instar de ses concurrentes, elle est poussée à s'associer pour rationaliser sa production et investir. Elle fusionne ainsi avec la Société Métallurgique de Knutange (SMK), une usine sidérurgique de taille comparable.
Le nouvel ensemble, constitué en , s'appelle Société Mosellane de Sidérurgie (SMS). Il concentre les mines de fer, les deux usines intégrées d'Hagondange et de Knutange, la fonderie d'Ars-sur-Moselle et les fours à chaux de Dompcevrin. Avec une production de 4,8 Mt de minerai, 5,6 Mt de fonte et 1,6 Mt d'acier en 1962, c'est la 5e plus grande société sidérurgique française. L'opération est rationnelle mais la dimension obtenue reste insuffisante pour élaborer un programme d’investissements à la hauteur des nécessités. Un mois plus tôt, le HF6 avait été définitivement arrêté.
En 1965, l'usine met en service deux convertisseurs à l'oxygène de 45 t, à soufflage par le fond de type LWS, grâce à la modernisation de deux de ses convertisseurs Thomas.
Le , la SMS fusionne avec l’Union Sidérurgique Lorraine, de Wendel et Cie et Sidélor, pour créer Wendel-Sidélor. Cette fusion coordonne les usines mosellanes de produits longs, mais acte le déclin à long terme de l'usine. En effet, de Wendel et Cie et Sidélor s'étaient associées en 1964 dans Sacilor, afin de concentrer toute la production de produits longs dans un unique ensemble énorme et ultra-moderne : l'usine sidérurgique de Gandrange-Rombas.
La position de l'usine d'Hagondange devient délicate : elle ne lamine que des produits longs (poutrelles, rails, fers marchands) dont l'importance décline structurellement. De ce carnet, 25 % sont des produits de qualité élaborés aux convertisseurs Martin. Mais, en 1971, l'acier de qualité identique élaboré dans les convertisseurs à l'oxygène de l'aciérie de Gandrange étant plus compétitif, l'aciérie Martin est arrêtée définitivement. Les 75 % restant sont élaborés aux convertisseurs Thomas ou LWS. Or la qualité de l'acier Thomas est dépassée. Celle-ci peut-être améliorée dans un « four à canal », un pilote de four d'affinage continu, qui est dédoublé et industrialisé en 1974 afin de pouvoir traiter 300 à 360 kt/an d'acier. Mais malgré ses résultats prometteurs, la technologie arrive au mauvais moment.
En effet, en 1974, alors que la crise de la sidérurgie dans le bassin lorrain va atteindre son paroxysme, le HF2, qui ne sert que de réserve depuis plusieurs années, est définitivement arrêté. Le complexe d'Hagondange fabrique, à partir de minette lorraine, un peu moins d'un million de tonnes de produits longs. Il met en œuvre 4 laminoirs :
Les HF1 et HF3 sont arrêtés en 1977 et 1978. Cette année-là, avec 2 ou 3 hauts fourneaux, l'UCPMI produit encore 670 129 t de fonte. La productivité s'est donc améliorée mais, au cours des années 1960 et 1970, il est devenu évident que sans gros convertisseurs à l'oxygène, coulée continue et train continu, un site sidérurgique n'a aucun avenir. Ces trois technologies sont incontournables ; aucune n'est adoptée. La cohérence du site est paradoxalement un handicap : une amélioration par étapes le désorganiserait plus qu'elle ne le pérenniserait. Mais au même moment, les usines littorales de Fos-sur-Mer et de Dunkerque tournent à plein régime en employant du minerai riche importé.
Le , les deux derniers hauts fourneaux, les HF3 et HF4 sont éteints. Quelques semaines plus tard, l'usine d'agglomération est arrêtée, suivie de la cokerie à la fin de l'année. Fin 1980, seul le train à petit profilé marche encore, le blooming et l'aciérie Thomas venant de s'arrêter. Le dernier laminage se déroule le . L’usine ferme officiellement deux jours après. La voisine SAFE, encore propriété de Renault mais bientôt revendue à Usinor qui en fait le noyau de la future Ascometal, est restée à l'écart de ces restructurations. En 2019, c'est le seul vestige de l’activité sidérurgique à Hagondange.
La reconversion de la friche industrielle devient un dossier symbolique. Quatre ans après, le , le parc d'attractions Big Bang Schtroumpf ouvre sur le terrain anciennement occupé par l'usine.
Owlapps.net - since 2012 - Les chouettes applications du hibou