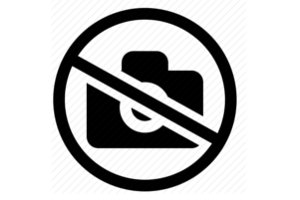
The Pratt & Whitney J57 (company designation: JT3C) is an axial-flow turbojet engine developed by Pratt & Whitney in the early 1950s. The J57 (first run January 1950) was the first 10,000 lbf (45 kN) thrust class engine in the United States. It was also the first two-spool turbojet to run, a few months before the similar Bristol Olympus in the UK.
The J57/JT3C was developed into the J52 turbojet, the J75/JT4A turbojet, the JT3D/TF33 turbofan, and the XT57 turboprop (of which only one was built). The J57 and JT3C saw extensive use on fighter jets, jetliners, and bombers for many decades.
The J57 was a development of the Pratt & Whitney XT45 (PT4) turboprop engine that was originally intended for the Boeing XB-52. As the B-52 power requirements grew, the design evolved into a turbojet, the JT3.
Pratt & Whitney designed the J57 to have a relatively high overall pressure ratio to help improve both thrust-specific fuel consumption and specific thrust, but it was known that throttling a single high pressure ratio compressor would cause stability problems. As Sir Stanley Hooker explains in his autobiography, the outlet area of a compressor is significantly smaller than that of its inlet, which is fine when operating at the design pressure ratio, but during starting and at low throttle settings the compressor pressure ratio is low so ideally the outlet area should be much larger than its design value. Put crudely the air taken in at the front cannot get out the back, which causes the blades at the front of the compressor to stall and vibrate. The compressor surges, which normally means the airflow reverses direction, causing a sharp drop in thrust.
By the late 1940s, three potential solutions to the stability problem had been identified:
1) bleeding any excess compressed air at part speed overboard through interstage blow-off valves
2) incorporating variable geometry in the first few stages of the compressor
3) splitting the compressor into two units, one of which supercharges the other, with both units being mounted on separate shafts and driven by their own turbine
GE adopted the second option with their General Electric J79, while Pratt & Whitney adopted the two-spool arrangement with their J57.
P&W realized that if they could develop a modest pressure ratio (< 4.5:1) axial compressor to handle adequately at any throttle setting including starting and acceleration, they could put two such compressors in series to achieve a higher overall pressure ratio.
In a two-spool arrangement, the first compressor, usually called Low Pressure Compressor (LPC), is driven by the Low Pressure Turbine (LPT), and supercharges another unit known as the High Pressure Compressor (HPC) itself driven by the High Pressure Turbine (HPT). During starting the HP spool starts to rotate first, while the LP spool is stationary. As the HP spool accelerates and the fuel:air mixture in the combustor lights up, at some point there is sufficient energy in the turbine gas stream to start to rotate the LP spool, which accelerates, albeit more sluggishly. Eventually, at full throttle, both spools will rotate at their design speeds. Because the exit temperature of the HPC is obviously higher than that of the LPC, a similar blade tip Mach number for both units is achieved by making the design HP shaft speed significantly higher than that of the LP shaft. Any reductions in compressor diameter going towards the combustor exaggerates the difference.
In the same timeframe as the J57, the Bristol Aeroplane Company Engine Division in the UK also adopted the two-spool arrangement into their Olympus turbojet engine series, which went on to propel the Avro Vulcan bomber and later the Concorde. Within a few months, both P&W and Bristol had had a first run of their prototypes. Both demonstrated superb handling.
Today, most civil and military turbofans have a two spool configuration, a notable exception being the Rolls-Royce Trent turbofan series which has three spools.
Incidentally, most modern civil turbofans use all three of the above options to handle the extremely high overall pressure ratios employed today (50:1 typically).
During the 1950s the J57 was an extremely popular engine, with numerous military applications. Production figures were in the thousands, which led to a very reliable engine. Consequently, it was only natural for Boeing to choose the J57 civil variant, the JT3C, for their 707 jetliner. Douglas did likewise with their DC-8. Pressure to reduce jet noise and specific fuel consumption later resulted in P&W using an innovative modification to convert the JT3C turbojet into the JT3D two spool turbofan, initially for civil purposes, but also for military applications like the Boeing B-52H. The prestigious Collier Trophy for 1952 was awarded to Leonard S. Hobbs, Chief Engineer of United Aircraft Corporation, for "designing and producing the P&W J57 turbojet engine". The engine was produced from 1951 to 1965 with a total of 21,170 built.
Many J57 models shipped since 1954 contained 7-15% of titanium, by dry weight. Commercially pure titanium was used in the inlet case and low pressure compressor case, whereas the low pressure rotor assembly was made up of 6Al-4V titanium alloy blades, discs and disc spacers.
Titanium alloys used in the J57 in the mid-50s suffered hydrogen embrittlement: 412 until the problem was understood.
On May 25, 1953, a J57-powered YF-100A exceeded Mach 1 on its first flight.
Data from:Aircraft Engines of the World 1964/65, Aircraft engines of the World 1957
Data from
Data from Flight
Related development
Comparable engines
Related lists
Owlapps.net - since 2012 - Les chouettes applications du hibou